Products
- Metal Casting
- Die Casting
- Sand Casting
- Gravity Casting
- Investment Casting
- Non Ferrous Casting
- Metalworking Service
- Metal Fabrication
- Sheet Metal Fabrication
- Metal Welding
- Metal Cutting
- Metal Bending
- Metal Plate Rolling
- Metal Roll Forming
- Metal Stamping
- Deep Drawn Stamping
- Expanded Sheet Metal
- Metal Perforating
- Plastic Molding
- Injection Molding
- Rotational Molding
- Blow Molding
- Thermoforming
- Precision CNC Machining
- EDM Machining
- Heat Treatment
- Surface Treatment
Plastic Blow Molding
Blow molding is a highly developed molding technology, it is best suited for basically hollow parts (such as plastic bottles) with uniform wall thicknesses, where the outside shape is a major consideration. The blow molding are widely used in bottles, containers, liquid soap, shampoo, motor oil tank, drums, tubs, and storage tanks.
Plastic Blow Molding Products Samples
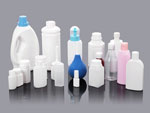
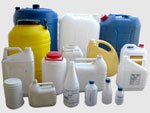
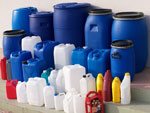
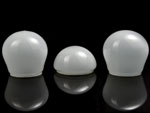
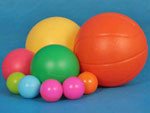
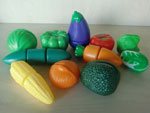
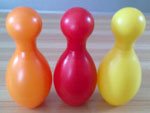
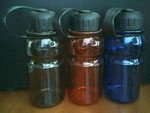
Blow molded parts can be formed from a variety of thermoplastic materials, including the following:
1. Low Density Polyethylene (LDPE)
2. High Density Polyethylene (HDPE)
3. Polyethylene Terephthalate (PET)
4. Polypropylene (PP)
5. Polyvinyl Chloride (PVC)
Our Capabilities:
Wall-Thickness: 0.1mm ~ 8.0mm
Product Size Range: 10mm ~ 1,500mm
Product Weight Range: 0.05kg ~ 50.00kg
Extrusion Bottle Blow Molding:
In extrusion blow molding, plastic is melted and extruded into a hollow tube. This parison is then captured by closing it into a cooled metal mold. Air is then blown into the parison, inflating it into the shape of the hollow bottle, container or part. After the plastic has cooled sufficiently, the mold is opened and the part is ejected. Continuous and Intermittent are two variations of Extrusion Blow Molding. In Continuous Extrusion Blow Molding the parison is extruded continuously and the individual parts are cut off by a suitable knife.
Examples of parts made by the extrusion bottle blow molding process include dairy containers, shampoo bottles, hoses/pipes, and hollow industrial parts such as drums.
Basic Process:
1. A thermoplastic resin is heated to a molten state.
2. It is then extruded through a die head to form a hollow tube called a parison.
3. The parison is dropped between two mold halves, which close around it.
4. The parison is inflated.
5. The plastic solidifies as it is cooled inside the mold.
6. The mold opens and the finished component is removed.
Maxtech is a professional plastic blow mold manufacturer in China. We offer a reliable and low cost plastic blow molding solution for materials of LDPE, HDPE, PET, PP, PVC.
We also provide the following services:
1. Metalworking Service, CNC Machining and EDM Machining Service
2. Heat Treatment:
Hardening, Annealing, Normalizing, Stress Relieving, Softening, and Graphitization
3. Surface Treatment:
Metal Polishing (Metal Mirror Polished, Brushed Metal Finishing), Shot Blasting, Sandblasting, Spray Painting, Powder Coating, Thermal Spraying, Anodizing, Chrome Plating, Nickel Electroplating / Electroless Nickel Plating, Hot-Dip Galvanizing, Copper Plating, Phosphorizing, Electrophoresis and Passivation
4. Assembly
5. Packing
6. Testing Report, QC Report